When soldering through-hole components onto a PCBA, you need to ensure the lead-to-hole diameter ratio meets IPC standards.
IPC standards refer to the guidelines that ensure reliable and consistent connections in electronic assemblies.
For example, IPC-2581 provides a standardized format for exchanging design data between PCB designers and manufacturers, while IPC-2221 is a general standard for PCB design.
This post covers the essential aspects of these standards and provides tips to ensure your through-hole components meet the required fill ratios.
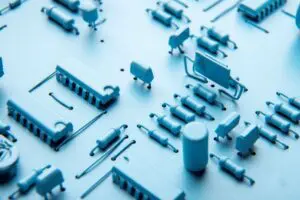
(freepik/Freepik)
Optimizing Lead Length for Low-Profile Designs
In low-profile products, where SMD components often dominate, some boards still require through-hole components. However, the lead length on these parts often exceeds the PCB’s thickness.
To maintain a compact profile—especially in stacked boards—you may need to trim the leads to keep them from protruding beneath the PCB. In some cases, you must trim the leads to match the board’s thickness.
For example, pin headers often come with leads that don’t extend through the board. As per IPC-A-610, you can’t solder the pads on the underside when leads fail to extend.
Ensuring Proper Solder Coverage for Through-Hole Components
Did you know that leads on through-hole components need enough solder to stay securely in place? This issue becomes even more critical when the lead doesn’t extend fully through the PCB, as it leaves no solder on the underside for reinforcement.
Consider two scenarios: when the lead extends beyond the board’s thickness and when you trim the lead shorter. The J-STD-001 and IPC-A-610 standards provide specific guidelines for both cases, ensuring proper soldering and secure connections.
Achieving the Right Solder Joint Fit
To get a reliable solder joint, the clearance has to be right. If it’s too tight, solder won’t flow properly—heat won’t spread, and the connection weakens. But if the gap’s too wide, the joint might lose its strength, and you could end up with solder bridging.
IPC-2221 recommends a 0.2 to 0.25 mm gap between the lead and hole. Stay in that range, and you’ll have a sturdy, reliable joint.
Controlling Solder Application
With short leads, controlling solder paste application is crucial. One way to manage this is by minimizing the paste mask opening during the stencil application process—a standard practice in lead-free PCB assembly services. If reducing the paste mask opening isn’t feasible, specifying a reduction in volume in the assembly instructions is another approach.
For long leads, wetting requirements in plated through-holes don’t usually need to be detailed. Instead, you can refer to a specific standard, and the assembler can determine what’s required. They can also suggest any necessary design adjustments. Using an automated dispenser will help you achieve consistent solder application.
Ensuring Compliance
Short leads can still meet IPC standards if you meet specific conditions. Leads shorter than the board’s thickness can qualify. Additionally, when the lead shoulders or components sit flush with the board, the lead ends don’t need to be visible in the solder joint.
The key is ensuring that the plated through-hole barrel fill meets the required standards. If the leads don’t extend beyond the board, you must achieve a fill ratio of at least 75% to comply with IPC guidelines.
Long leads that extend fully through the board and may protrude beyond it require proper solder wetting and coverage to ensure a reliable connection. According to IPC-A-610, the standard doesn’t strictly require the lead to protrude beyond the board by a certain length. However, it emphasizes that the solder joint must be complete, with sufficient fill in the plated through-hole.
IPC-A-610 Classifications
IPC-A-610 provides different classifications (Class 1, 2, and 3) based on the quality and reliability of the solder joints.
Class | Description | Typical Applications |
---|---|---|
Class 1 | Focuses on basic functionality. Aesthetic flaws and minor imperfections are acceptable as long as the product works. |
Consumer electronics, toys, simple appliances. |
Class 2 | Balances performance with durability. Moderate imperfections are allowed, but the product should reliably function over time. |
Everyday electronics, industrial controls, office equipment. |
Class 3 | Demands the highest quality and reliability. No room for errors or imperfections, as these products are used in critical applications. |
Aerospace, medical devices, military equipment. |
Always check the class before you begin soldering to ensure you meet the right specifications.
Role of IPC-7711/7721 in Rework and Repair
The guidelines you follow during rework and repair can really affect the reliability of your assemblies. Some defects can be fixed easily, while others might compromise the entire board. Sticking to the right standards means your assemblies will maintain their integrity.
You don’t have to guess how to rework solder joints correctly. Standards like IPC-7711/7721 give you detailed procedures to follow. IPC-7711/7721 helps you address defects by providing guidelines on everything from component removal to solder reflow.
Once you identify the issue, you can apply the correct method to fix it without risking the overall performance. IPC-7711/7721 also ensures that reworked joints meet the same high standards as the original ones. With this guidance, you can make sure your assemblies remain reliable, even after rework.
Conclusion
These are some of the IPC standards you need to know.
Whether you’re working in EMS PCB assembly or another area of electronics manufacturing, following the correct plated through-hole fill ratio can improve the strength and durability of your assemblies.
Start by evaluating your current soldering practices and make adjustments where needed to ensure compliance with IPC criteria.